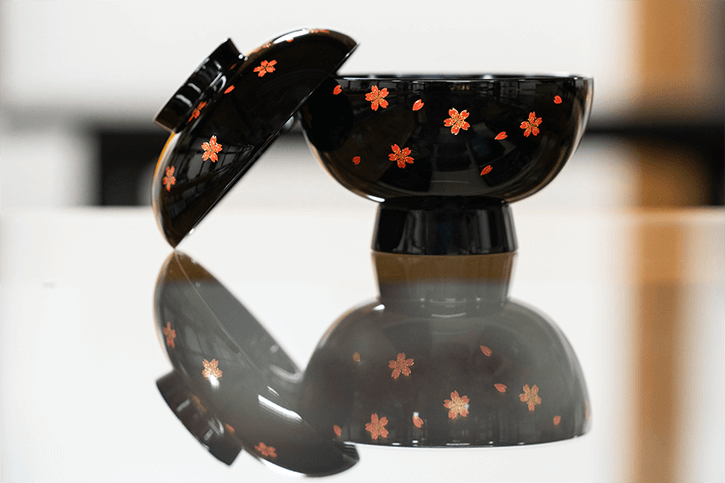
In a nondescript two-story building on the outskirts of Wajima, Ishikawa Prefecture, craftspeople are bent over their workstations, seemingly oblivious to the heat. As they coat and polish tableware, the room rings with the rasp of sandpaper, echoing the cicadas buzzing outside. This is the slow, painstaking work of producing Wajima lacquerware, or Wajima-nuri, a craft product of exquisite beauty from the Sea of Japan.
-
For centuries, people in China, Korea and Japan have been using the sap of the Chinese lacquer tree (Toxicodendron vernicifluum) and related species to create a hard, shiny coating that makes wooden objects durable and waterproof. Lacquerware in Japan, or shikki, is distinguished by its gorgeous decorative finish often featuring designs executed in maki-e sprinkled gold or silver powder.
The high gloss on Wajima ware is the result of multiple layers of polished lacquer
Wajima is one of Japan’s 23 centers for lacquer, but the craft takes pride of place here: out of a population of some 23,000, nearly 6,000 are involved in the lacquerware industry. In 1977, the Japanese government designated their traditional craft an Intangible Cultural Property, ensuring its time-honored methods are upheld and protected.
At Taya-Shikkiten’s showroom across the road from its workshop, plates and bowls finished in deep vermilion, black and gold sparkle in the display cases. There are traditional bowls, trays, bento boxes and chopsticks as well as more modern applications of lacquer such as wristwatches and fountainpens. Their glossy beauty is even more striking when one realizes they are all made by hand.Takahiro Taya is the 10th generation head of Taya-Shikkiten, founded in 1818
“We cannot automate our production process because the climate and humidity affect the lacquer and will change the results,” says Takahiro Taya, the 10th generation head of Taya-Shikkiten. “Also, the finish including the patterns are not something that can be achieved with a machine.”
Taya-Shikkiten was established by craftsman Taya Kihei in 1818, when the Maeda samurai clan ruled the Kaga Domain including Wajima and the Noto Peninsula. In the 19th century, the Taya family would carry their precious wares over the mountains to markets in Edo (today’s Tokyo) and Osaka. Today, they sell through online and bricks-and-mortar shops, but little in their production method has changed.Producing quality lacquerware is a labor-intensive process that cannot be automated
Creating Wajima lacquerware is a lengthy, complex process involving 124 stages and 6-7 different artisans. It begins when crafts workers carve out a block of asunaro wood, a kind of evergreen tree. It is smoked and dried for a year so that all moisture is removed, improving its durability. This is enhanced with a transparent base coat of lacquer.
Next, a mix of lacquer, baked earth and rice glue is applied to the ends of the wooden base. It’s during this process that an important feature of Wajima lacquerware is added: baked diatomaceous earth (jinoko). This is a light, chalk-like sedimentary rock that contains fossilized algae, making it very absorbent. The entire surface is then sanded down with a grinding stone.Wajima lacquerware is coated with a mix of lacquer and diatomaceous earth, which enhances durability
The process of adding lacquer layers and polishing them is repeated several times. A coat of purer lacquer is applied, and then the object is dried and hardened in a cedar storage room. Another feature of Wajima ware is that only natural lacquer is used, not synthetic, Taya points out.
“Polishing can involve the use of stones, charcoal and sandpaper,” says Satomi Hira, a veteran Taya-Shikkiten worker who polishes the many coats of lacquer. “It’s essential to ensure there are no small holes in the lacquer layers for a smooth finish.”
For the finish, a top coating of filtered lacquer is painted on in a dust-free room to avoid imperfections. Bright colors are especially challenging. Even if the same mix of pigment and lacquer is used, the resulting color can change depending on temperature, humidity and light exposure.Tsutomu Taya, 86, is a master craftsman with nearly 70 years’ experience creating lacquerware
For objects with decorative elements, crafts workers apply maki-e powder, or add extra carving, lacquer and gold elements for features known as chinkin, or “sunken gold.” Once the finishing is complete, the lacquer product is ready for a lifetime of service. Even if the object is damaged, it’s still useful.
“Because the base layer is very strong, Wajima lacquerware can be repaired,” says former head of Taya-Shikkiten Tsutomu Taya, 86, a master craftsman with nearly 70 years’ experience creating lacquerware. “We would like to continue this tradition of Wajima lacquerware and appeal to new customers both in Japan and overseas.”Photos courtesy of Ishikawa Prefectural Tourism League
The Wajima Museum of Urushi Art features Wajima lacquerware including works by Living National Treasure artists. Photos courtesy of Ishikawa Prefectural Tourism League
To get a deeper understanding of the history and development of Wajima lacquerware, visit the Wajima Museum of Urushi Art. It showcases Wajima lacquerware including works by Living National Treasure artists, as well as lacquerware from other areas of Japan and overseas.
Taya-Shikkiten (www.wajimanuri.co.jp) is located at:
Address: Emisiana 55, Sugihiramachi, Wajima-shi, Ishikawa Prefecture
It is about a 30-minute walk or 7-minute taxi ride from the Wajima Museum of Urushi Art (www.art.city.wajima.ishikawa.jp/en), which is located at:
Address: 11 Shijukari, Mitomorimachi, Wajima-shi, Ishikawa Prefecture- Wajima Museum of Urushi Art (lacquer art museum)
-
4.0
41 Reviews -
-
- Ishikawa Pref. Wajimashi Mitomorimachi Shijugari 11
-
-
-
- 0768229788
-
-
-
- 9:00-17:00(Latest entry16:30…
-
View All